The molecular weight of a polyether polyol, which represents the average size of its molecules, has a significant impact on the properties of the final polyurethane. For example, conventional flexible slabstock foams, commonly used in furniture and bedding, typically utilize triols (polyols with three hydroxyl groups) with molecular weights ranging from 3,000 to 4,000. This specific molecular weight range contributes to the desired softness and flexibility of these foams.
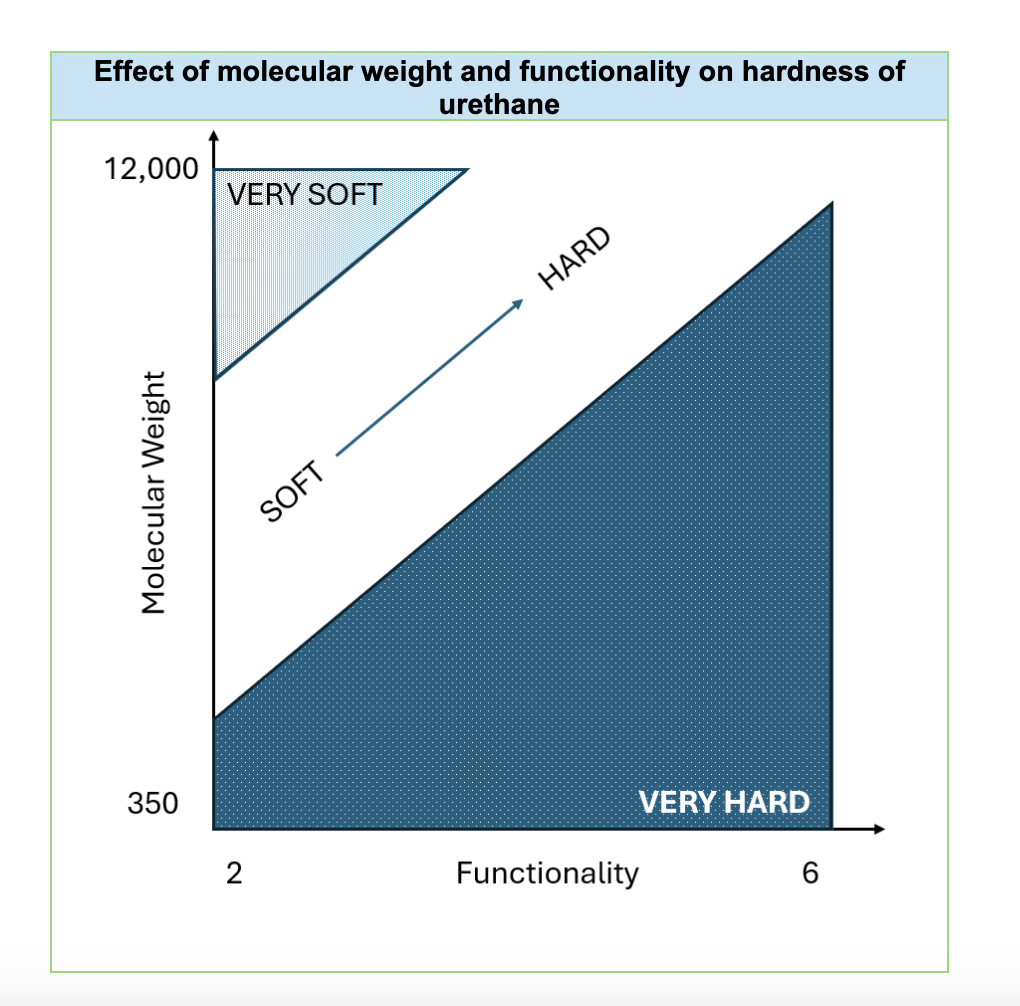
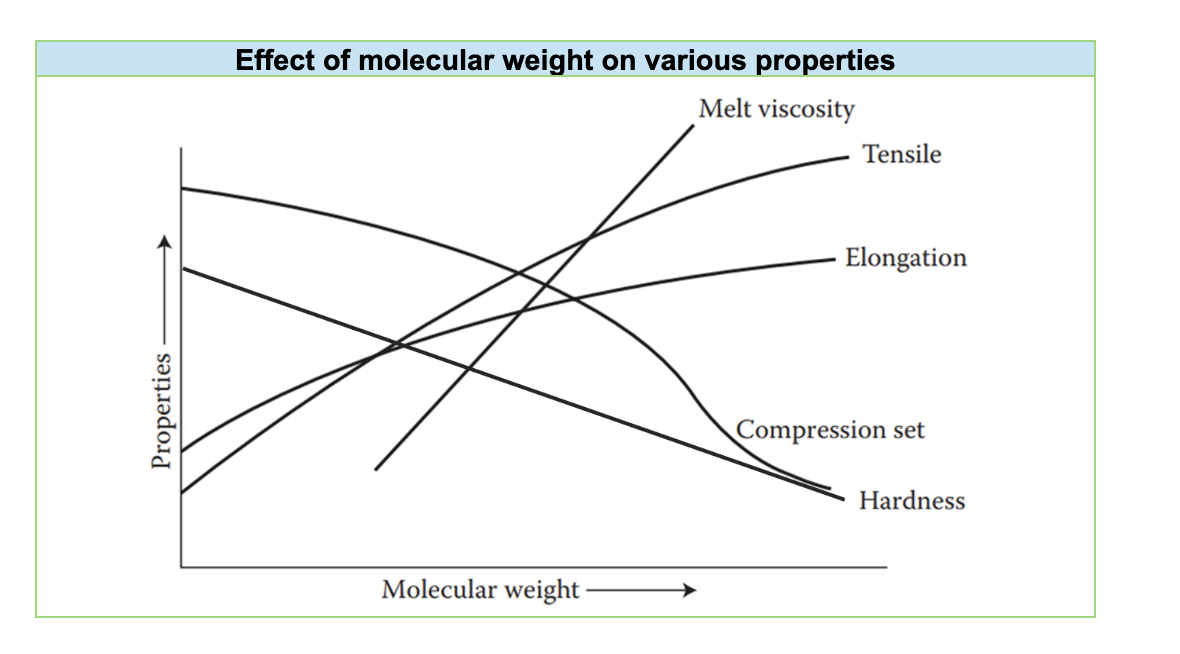
Functionality, representing the average number of hydroxyl terminal groups per polyol molecule, is another crucial factor influencing foam properties. Higher functionality polyols, those with more hydroxyl end-groups, generally lead to harder and more rigid foams. However, increasing functionality can sometimes compromise other mechanical properties like tensile strength, tear resistance, resiliency and elongation. Therefore, selecting the appropriate functionality is essential to achieve the desired balance of hardness and other performance characteristics.
Hydroxyl Functionality |
Flexible Foam |
Rigid Foam |
CASE |
2 |
•• |
• |
•• |
3 |
•• |
•• |
• |
4 |
•
|
•• |
|
5 |
|
•• |
|
Hydroxyl group position plays a big role in the reactivity of the polyol. Primary hydroxyl (OH) groups are located at the end of the molecule's chain, while secondary hydroxyl groups are located within the carbon chain. The primary hydroxyl group reacts much more rapidly with isocyanates than the secondary hydroxyl group. The performance of the polyols will be influenced by the ratio of primary to secondary hydroxyl group content.
Primary Component of Polyol |
Hydroxyl Group Position |
Reactivity |
Propylene Oxide (PO) |
Secondary OH |
Slow Reacting |
Mixed Propylene / Ethylene Oxide |
Primary / Secondary OH |
Medium Reacting |
Ethylene Oxide (EO) Tipped |
Primary OH |
Fast Reacting |
The hydroxyl value (OHV) quantifies the concentration of hydroxyl groups in a polyol, reported as milligrams of KOH equivalent to the hydroxyl content in one gram of the polyol. This value directly correlates with the reactivity of the polyol with isocyanates. Higher hydroxyl values indicate greater availability of reactive sites, which is critical in fine-tuning hard segments and crosslink density and mechanical properties in polyurethanes. Selecting an appropriate hydroxyl value is key to balancing processing efficiency and final product performance.
The acid value of a polyol measures the residual acidity present in the material, expressed as the milligrams of potassium hydroxide (KOH) required to neutralize the acidic components in one gram of the polyol. A low acid value is desirable in polyurethanes to minimize the side reactions with isocyanates during the curing process, ensuring a more controlled and predictable polymerization. Elevated acid values can lead to undesired catalytic effects, affecting foam chemical stability and mechanical properties.