Polytetramethylene Ether Glycol (PTMEG) is the premier polyether polyol used worldwide in the manufacture of high-performance polyurethane elastomers. Known for its unique performance attributes and processing advantages, PTMEG is used in a variety of applications across multiple industries.
These applications include polyurethane and polyurea resins, prepolymers, coatings, adhesives, cast polyurethane resins, TPUs, spandex fibers, and more. Compared with PPG-based polyols, PTMEG-based polyurethanes exhibit strain-induced crystallization in the soft segments and exact di-functionality, leading to significant enhancements in performance.
Processors know PTMEG as a high-performance polyol capable of formulating polyurethane elastomers in several positive directions with regard to desired product attributes. PTMEG will enhance polyurethane elastomer performance with respect to flexibility, dynamic properties, resiliency/rebound, hydrolytic stability, and abrasion resistance. Some PTMEG-MDI systems can be formulated to be FDA wet and dry food-approved.
PTMEG-based polyurethanes exhibit the following attributes:
|
|
|
|
|
|
|
|
For more than 15 years, Gantrade has supplied performance-enhancing polyols for a variety of industry applications worldwide. Our team of technical experts ensures that we match our product line of polycaprolactone polyols and PTMEG polyols to fit our customers’ exact specifications.
Polycaprolactones polyols demonstrate many of the unique performance characteristics of PTMEG in polyurethanes
Polycaprolactone polyols comprise a special class of aliphatic polyester polyols, used as the soft block segment of high-performance polyurethane elastomers. We can produce polycaprolactone polyols with very low acid values (increasing hydrolytic stability and controlled reactivity); perfect end-group functionality (controlled reactivity and improved network formation); narrow molecular weight distributions (low viscosity, including in the prepolymer form); and low glass transition temperatures (flexibility at low temperatures). Polycaprolactone-based polyurethanes incorporate many of the benefits assigned to PTMEG polyols, such as good hydrolytic stability in wet environments, low temperature flexibility, excellent toughness and abrasion resistance, excellent flex-fatigue life, durability, and good elastic memory. In addition, polycaprolactone-based PURs are much tougher materials than polyether-based PURs, and they exhibit higher temperature properties.
The price differences between the PTMEG and polycaprolactone polyols have normalized in the current global market. Hence, polycaprolactone polyols are being considered in conventional PTMEG applications, particularly in applications which do not require the superior resiliency, rebound and hysteretic properties of the PTMEG systems.
Polyurethanes based on polycaprolactone polyols exhibit the following property profiles, many of which are best-in-class performance attributes:
|
|
|
|
|
|
|
|
|
|
|
|
Structure-Property Profiles of Polyurethane Elastomers vs. Polyol Type
The chart below is a qualitative delineation of the relative performance of PTMEG and polycaprolactone polyols in polyurethane elastomers. The designation of “best-in-class” refers to the highest performance within the general classifications of polyurethanes.
Property/Polyol Class |
Polycaprolactone |
PTMEG |
Hydrolytic Stability: General Water Immersion |
VG E |
B VG |
Chemical Resistance |
B |
VG |
Low-Temp. Flexibility |
VG |
B |
Elevated Temp. Stability |
B |
VG |
Tensile Strength |
B |
E |
Resiliency & Rebound |
VG |
B |
Dynamic Properties |
E |
B |
Abrasion Resistance: Impingement Sliding |
VG B |
B VG |
Cut and Tear Strength |
E |
B |
Processing |
E |
B |
Hydrolytic stability
Hydrolytic stability of the PTMEG polyether structure is superior to the ester linkage; however, when immersed in water, the polyethers absorb water and are plasticized, losing mechanical properties. In water immersion applications at lower temperatures, the polycaprolactone polyols are preferred, furthered by their overall significantly higher tensile properties. Chemical resistance relates to oils, fuels, and hydrocarbon solvents. There are two types of abrasion resistance are sliding and impingement. Sliding refers to scraping and rubbing abrasion while impingement refers to particles striking the urethane surface. Polycaprolactone-based polyurethanes display higher tensile and tear resistance and exhibit excellent sliding abrasion resistance. This dynamic makes them ideal for applications like belt scraper blades and chute liners. PTMEG, due to its’s higher resiliency, offers better performance in applications where impingement abrasion is the dominant form of wear. This dynamic makes PTMEG based polyurethanes the choice for sandblast curtains and slurry pipe liners. Processing characteristics of polycaprolactone based urethanes are excellent, derived from the low polydispersity of the polycaprolactone polyols and the lower viscosities of the attendant prepolymers and TPUs.
Water Absorption Rates in TPUs
The water absorption rates for TPUs made from Placcel 220BT and PTMEG 2000 are compared in the graph below. The TPUs are based on polyol/MDI/BDO systems, prepared with Shore A Durometers of 88A-90A. Test pieces were dried at 80 °C for five hours and stabilized at 23 °C for 12 hours (50% RH) prior to immersion. The water absorption rate was measured from the weight pick-up data.
Placcel 220BT showed a lower water absorption rate than PTMEG 2000, which explains the tensile strength retention data after immersion in water at 80 °C in the bar chart below.
The spider diagram below summarizes comparative data for key performance indicators (KPIs) for the two polyols.
Placcel B vs. PTMEG based PURs: Key Performance Indicators
Placcel BDO-Initiated Series of Polycaprolactone Polyols
1,4-Butanediol-initiated polycaprolactone polyols (B-series) are linear structures that exhibit excellent soft-block phase separation and mechanical properties in a polyurethane. This family of polycaprolactone polyols mirrors many of the characteristics of the PTMEG polyols. The Placcel B-series of polyols exhibit outstanding hardness, tensile, tear properties, low glass transition temperatures (-45 to -48 °C), and the highest resistance to hydrolysis of the polycaprolactone polyols. They are available in multiple MW grades, including 1000 and 2000. For the counter to the liquid PTMEG 220 and 650, Placcel 204B (MW400) and 205U (MW 530), both liquids at room temperature, are recommended.
Characteristics of PTMEG and Placcel Polycaprolactone Polyols
Product |
Molecular Weight |
Appearance, 25 °C |
Melting Point, °C |
Hydroxyl value, (KOH mg./g.) |
Acid Value, (KOH mg./g.) |
Viscosity, cps |
PTMEG 220 |
220 |
Liquid |
-5 |
515 |
≤0.05 |
90/25°C |
PTMEG 650 |
650 |
Liquid |
11-16 |
173 |
≤0.05 |
300/25°C |
PTMEG 1000 |
1000 |
Wax |
24 |
112 |
≤0.05 |
350/60°C |
PTMEG 1400 |
1400 |
Wax |
27 |
80 |
≤0.05 |
600/60°C |
PTMEG 2000 |
2000 |
Wax |
28 |
56 |
≤0.05 |
950/60°C |
Placcel 204B |
400 |
Liquid |
0-10 |
280 |
≤0.05 |
254/25°C |
Placcel 205U |
530 |
Liquid |
18-22 |
212 |
≤0.10 |
310/25°C |
Placcel 210B |
1000 |
Wax |
35-45 |
112 |
≤0.15 |
143/60°C |
Placcel 220BT |
2000 |
Wax |
48-51 |
56 |
≤0.03 |
435/60°C |
A comparison of the mechanical properties of MDI-based TPUs using Placcel 220BT and PTMEG 2000 is provided in the table below. The TPU formulation is as follows:
- Equivalent Ratios: Polyol/MDI/BDO: 1.0/3.0/2.0
- Isocyanate Index: 1.05
Performance of TPUs Made from 2000 MW Polyols
Property/Polyol Class |
Placcel 220BT |
PTMEG 2000 |
100% Modulus (MPa) |
4.9 |
4.6 |
Tensile Strength (MPa) |
62 |
54 |
Ultimate Elongation (%) |
630 |
680 |
Tear Strength-B (kgf/cm) |
75 |
89 |
Tabor Abrasion per 1000 Times (mg. loss) |
50 |
72 |
Elastic Recover (%) |
74 |
80 |
Compression Set, 100 °C x 70 Hr. (%) |
48 |
56 |
Tg (°C) |
-48 |
-66 |
Summary and Conclusions
The price differences between the PTMEG and polycaprolactone polyols have normalized in the current market. Hence, polycaprolactone polyols are being considered in PTMEG applications, particularly in applications which do not require the superior resiliency and hysteretic properties of the PTMEG systems.
Performance parameters of the BDO-initiated Placcel polycaprolactone diols stand out as viable options based on the following attributes of the Placcel B-series polyols:
-
The very good hydrolytic stability of the Placcel T-series, with their low acid values. The high tensile properties and low moisture uptake of the Placcel T polyols provide for good performance in water immersion at moderate temperatures.
-
The melting points of the BDO-initiated series of diols are higher than those of the PTMEG polyols; however, at 60 °C, the melt viscosities are lower, based on a much narrow molecular weight distribution (the MW distribution of the Placcel B-series is ~1.2 to 1.3 (Mw/Mn); the PTMEG polyols are generally 1.9-2.0 (Mw/Mn). This attribute leads to a more uniform distribution of the hard block segments in a Placcel B based PUR, which is highly beneficial.
-
While the melting points of the Placcel B diols are higher than those of the comparable PTMEG MW grades, MDI prepolymers based on Placcel diols tend to be liquid.
-
Placcel 204B (MW 400) and 205U (MW 550) are liquid diols, like PTMEG 220 and 650.
-
Low glass transition temperatures and good low temperature flexibility in PURs. The Tgs of the Placcel B grades are about -45 to -48 °C, while the Tgs of the PTMEG grades are in the range of -68 to -74 °C.
-
All Placcel PCL diols and PTMEG diols have exact primary hydroxy functionalities of 2.0 and low residual catalyst levels. These qualities promote consistent and controlled reactivity and open times.
-
The stress-strain profiles of the polycaprolactone polyols and PTMEG PURs are very similar, driven by the stress-induced crystallization characteristics of both soft blocks.
-
The linear BDO linkage in the Placcel B-series affords much higher Shore A hardness values, which is characteristic of PTMEG based PURs. Note: for lower Shore A hardness values we recommend the Placcel U-series, DEG-initiated.
-
PURs based on the Placcel B-series diols exhibit the highest tensile and tear properties, adhesive characteristics, and chemical, solvent, oil, and UV resistance.
-
Good tear, cut, and chip resistance can be achieved in both series of PURs.
-
Both polyol series exhibit good durability and abrasion resistance. The Placcel B grades show superior sliding abrasion resistance, while the PTMEG grades exhibit higher impingement abrasion resistance.
-
The PTMEG polyols produced elastomers with outstanding resiliency, rebound, and low hysteresis properties. Resiliency and hysteresis properties of the Placcel B are more intermediate in nature, but better than those of adipate based polyester polyols.
The Placcel B series of diols can provide parity to PTMEG polyols in performance and processing characteristics within many polyurethane finished product applications. Representative TPU performance data for polycaprolactone polyols versus PTMEG are compared in the chart below.
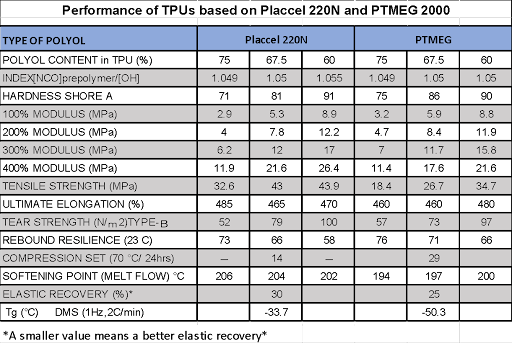
Polycaprolactone-based polyurethanes incorporate many of the benefits assigned to PTMEG polyols, such as good hydrolytic stability in wet environments, low temperature flexibility, excellent toughness and abrasion resistance, excellent flex-fatigue life, durability, and good elastic recovery. In addition, polycaprolactone based PURs are much tougher materials than polyether-based PURs.
To understand which polyol is best suited for your unique needs, partner with Gantrade. We are a global leader in the distribution of high-performance polyols for a variety of performance enhancements within multiple industry applications. Our team’s wealth of technical knowledge and expertise, along with our uncompromising standards for customer service, ensure that you will receive the best polyurethane solutions for applications. Gantrade’s urethane platform of specialty polyols, chain extenders, and curatives provide a broad range of possibilities to achieve your high-performance polyurethane requirements. Our global supply chain means high-quality chemical products where you need them, when you need them. Contact Gantrade to learn more.